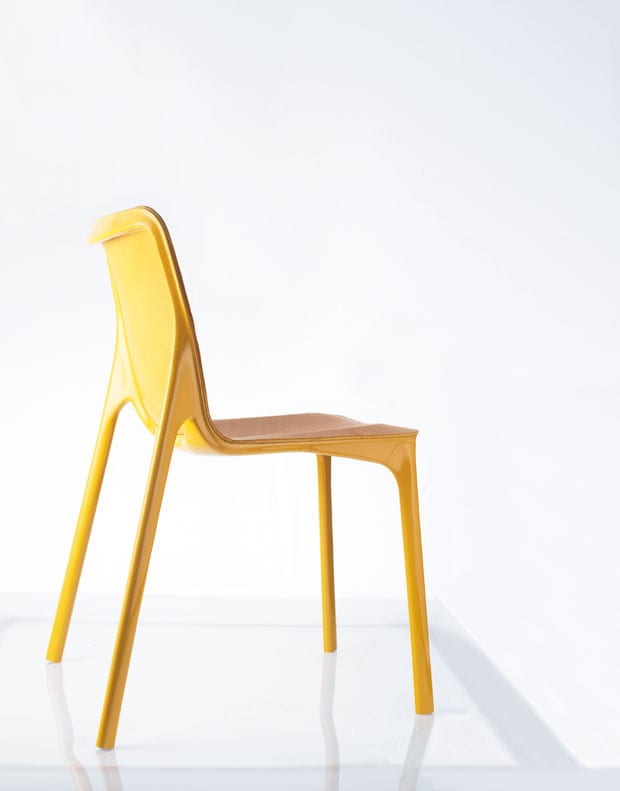
words Anna Bates
“With this chair we fulfil strict regulations that allow fat arses to sit on a delicate small chair,” says Munich-based designer Stefan Diez, quite matter-of-factly.
“It’s a real trouble,” he goes on, “to have a lightweight chair strong enough to take the kilos.” Diez’s sheet steel Chassis, for German furniture manufacturer Wilkhahn, was designed using technology and tools from the car manufacturing industry to achieve its shape – as lean and toned as an Olympic runner.
“We wanted to use sheet metal because it’s strong, and is much more advanced than casting technology,” says Diez. “You just have a skin, you don’t fill it up. With cast aluminium you would have thicker walls.”
Diez wanted to do a project that exploited Germany’s car manufacturing heritage. But after several rejections, he headed to Amsterdam with a cardboard and laser-sintered prototype in tow, where a car producer open to experimentation was waiting.
Here, the chair that Diez spent two years perfecting was instantly redesigned to make it more supportive. The figure-of-eight frame was altered so it could be stamped in one go, using a heavy press comprising two forms of hardened steel. In place of the original L-shaped profiles, the frame and legs were redesigned with stronger, ditch-shaped profiles. “Basically, the way the frame is constructed is exactly the same as a car piece,” Diez explains. “The exterior face of a car piece is like the chair from underneath,” he says, while the reverse, usually covered in textile material, is like the top of the seat. The leather seat will be connected to the frame (the joins neatly hidden in the ditches), similar to the way fabric is connected to the inside of a car. The four legs, stamped separately, will be soldered onto the seat.
The redesign process was achieved in record speed. Instead of making strength-testing prototypes, a computer file of the chair was handed to the engineer who calculated the precise strength.
“Using a car manufacturer doesn’t make it cheaper,” says Diez, “but it makes it more exciting. If you don’t get to do these things, designers will continue to make the same stuff. Maybe one day it will make things cheaper – the machines we used were already financed, and the tools exist.”
Still at prototype stage, the chair will go into production later this year with Wilkhahn; one of several manufacturers in the country slowly increasing in bravery thanks to Diez’s persistent challenging.